In the modern world of manufacturing and engineering, CNC machines are indispensable tools. Computer programs control them. They can complete high-precision and high-efficiency processing tasks. The same CNC machine type shows unique advantages when processing parts of different materials and shapes. It can meet the needs of the manufacturing industry for efficient, precise, and diverse processing.
We hope to provide you with a comprehensive guide. This article will take an in-depth look at all types of CNC machines. These include CNC milling machines, CNC lathes, and CNC grinders. We will analyze their working principles, application areas, and advantages. This article will give you a deeper understanding of the diversity of CNC machines.
Different Types Of CNC Machines
CNC machines control machine tool movement and processing processes digitally. It contains the movement of a tool or workpiece through pre-programmed instructions. It enables high-precision, high-efficiency processing. CNC machine tools can be divided into types according to structure and function. Here are some common CNC machine types.
Type 1: CNC Milling Machine
CNC milling machines are mainly used for cutting on the surface of workpieces. It uses a rotating tool to cut the workpiece at different angles and directions. It enables the processing of complex parts. Precisely control the movement of the tool through pre-written CNC code. It allows high-precision processing. CNC milling machines have different structures depending on the workpiece and processing requirements. Such as vertical, horizontal, gantry type, etc.
Applications
- Aerospace Industry: Used for machining plane parts. Such as wings, fuselage structures, and engine parts.
- Automotive Manufacturing: Used to manufacture auto parts. Including engine parts, chassis components, and body structures.
- Electronics Manufacturing: Used to process electronic components, circuit boards, and casings.
- Mold And Model Manufacturing: It is used to manufacture various molds and 3D models.
- Medical Device Manufacturing: Used to process high-precision medical device parts. Such as artificial joints and implants.
- Energy Field: Used to manufacture energy equipment components. Such as wind turbine parts and nuclear power equipment components.
- Custom Part Manufacturing: Due to its flexibility, CNC milling machines are often used to manufacture various custom parts. It is suitable for small-batch production.
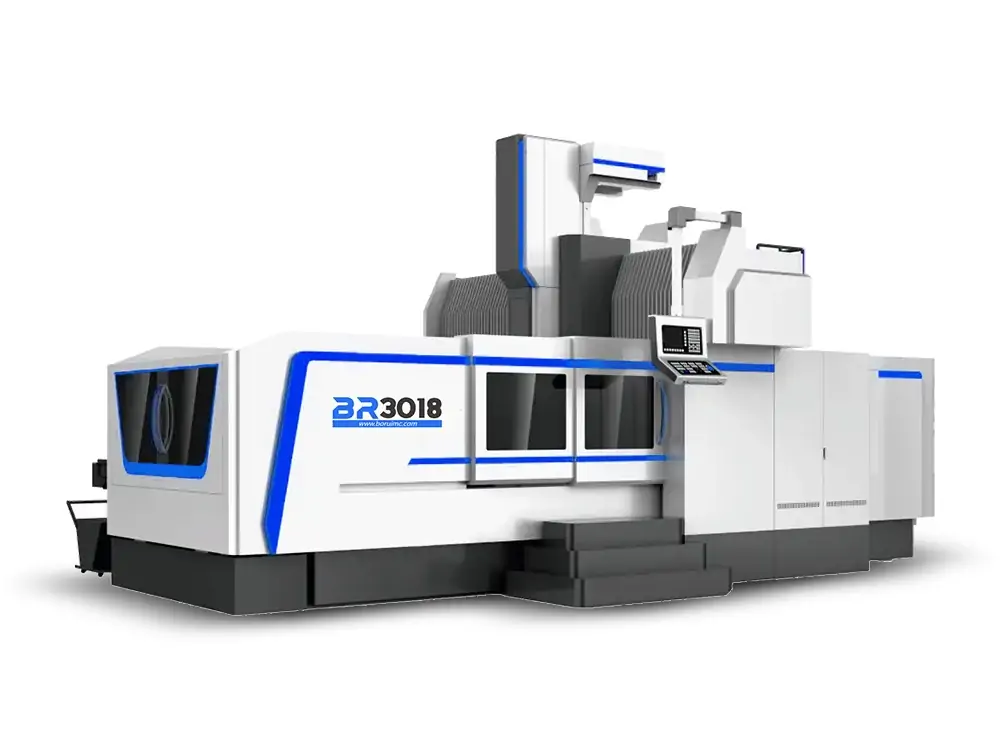
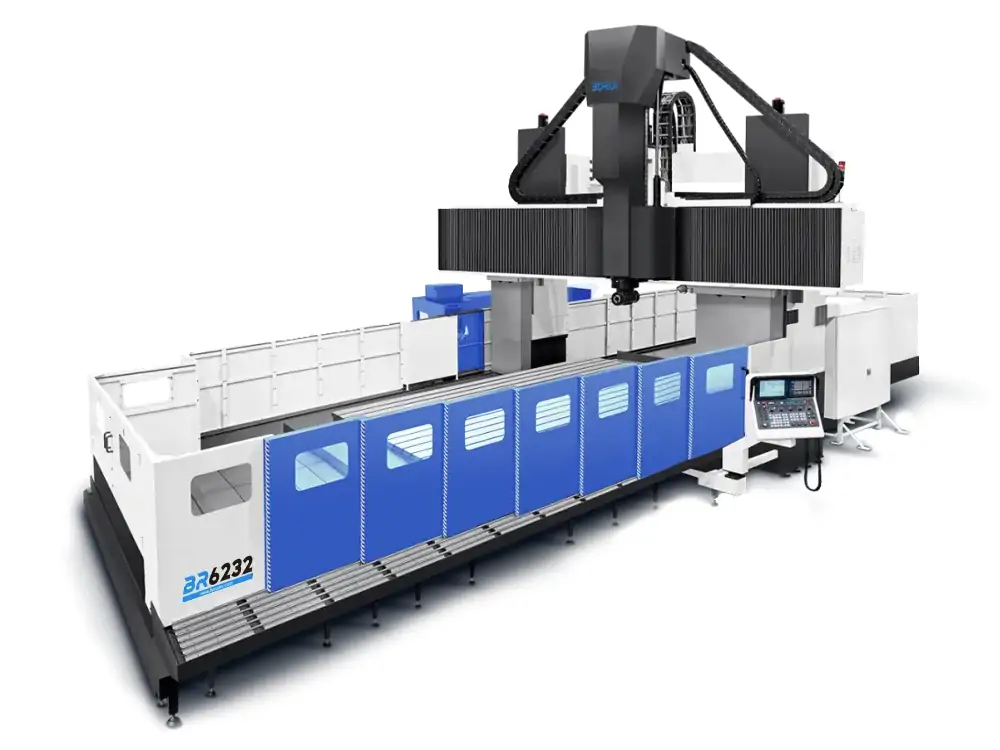
Pros
- High Precision: CNC milling machines are capable of high precision and repeatability. It ensures the accuracy of machined parts.
- High Efficiency: CNC milling machines have automated control and high-speed cutting capabilities. So it can complete complex processing tasks quickly. It can improve production efficiency.
- Flexibility: CNC mill machines can process different parts by modifying the CNC program. It provides production flexibility.
- Multi-axis Machining: Many CNC milling machines have multi-axis control capabilities. They can cut in many directions simultaneously. It is suitable for the machining of complex parts.
- Reduce Human Errors: It is controlled by a computer program. So, it can reduce the impact of human factors on processing quality and improve consistency.
Cons
- High Cost: Purchasing and maintaining CNC milling machines is high, especially for small or start-up businesses.
- Complex Operation: Operating a CNC milling machine requires specialized training. Operators need to understand CNC programming and machine tool operation.
- Difficulty in Maintenance: Once a failure occurs, professional technicians must repair and maintain it.
- Space Requirements: Larger CNC mills need larger workspaces. It may not be suitable for environments with limited space.
Type 2: CNC Lathes
CNC lathes are mainly used for cutting rotating workpieces. It controls the movement of the tool through a pre-written CNC program. It can complete processing operations such as outer circles, inner holes, and threads. CNC lathe machine is widely used in the manufacturing of shaft parts.
Applications
- Shaft Parts Manufacturing: CNC lathes are often used to manufacture shaft parts. Such as bearings, journals, and bushings.
- Thread Processing: CNC lathes can be used for high-precision internal and external thread processing. It is suitable for manufacturing threaded parts.
- Part Flipping Processing: CNC lathes can complete multi-sided processing on the same machine tool by flipping the workpiece. It can improve production efficiency.
- Cutting And Roughing: It is used for cutting, turning, grooving, and processing metals, plastics, and other engineering materials.
- Complex Shape Parts: It is suitable for processing difficult shape parts. Such as automobile crankshafts, gears, and cams.
- High-precision Parts Manufacturing: CNC lathes have high-precision control capabilities. It is widely used in the manufacturing of parts that need high precision. Examples include aerospace and medical equipment.
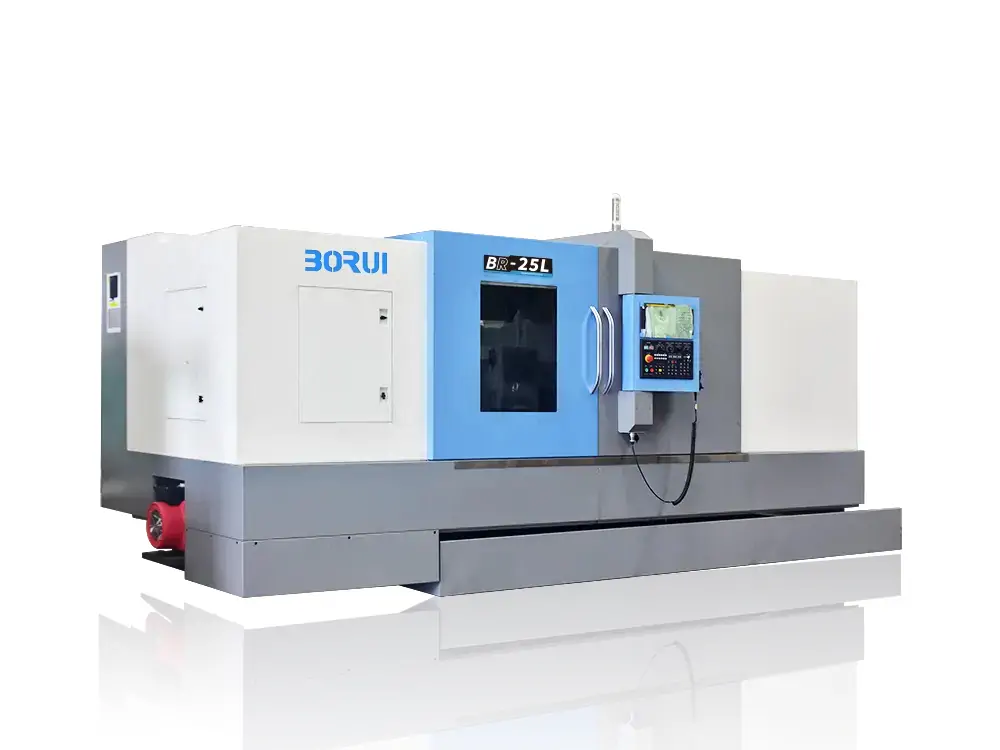
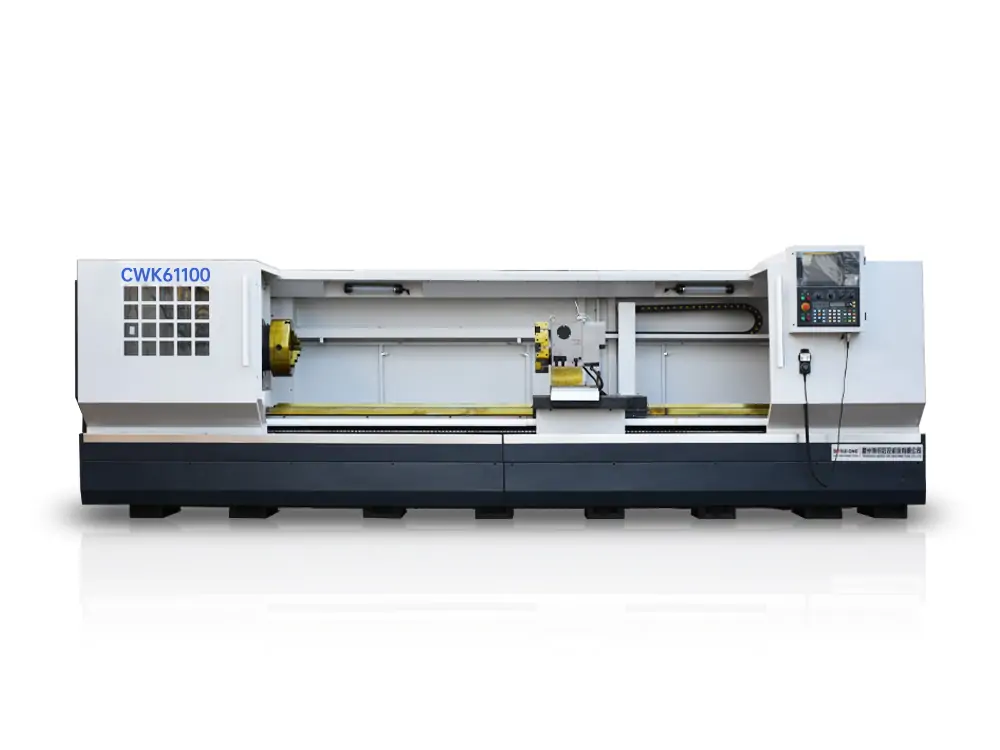
Pros
- High Precision: CNC lathes are capable of very high precision. It delivers consistent and reliable part processing.
- Automation: Automatic processing is realized through CNC program control. It reduces operator human error.
- Multi-function: It can perform multi-axis and multi-tool simultaneous processing. It is suitable for diverse and complex production tasks.
- High Efficiency: Automatic tool changing and high-speed cutting allow it to complete mass production in a short time.
- Flexibility: CNC lathes are suitable for producing many varieties and small batches of workpieces. The machine can adjust the processing program at any time.
Cons
- High Cost: CNC lathes are expensive to buy and maintain. It is not suitable for small-scale or start-up businesses.
- Complex Operation: Operating a CNC lathe requires specialized training. Operators need to understand CNC programming and machine tool operation.
- Difficulty in Maintenance: Once a failure occurs, professional technicians are required to repair and maintain it.
- Dependent on Power and Software: It relies on the power supply and stable CNC software operation. A power outage or software glitch could impact production.
Type 3: CNC Grinding Machine
CNC grinder machines are mainly used to grind the surface of workpieces to obtain high precision and smoothness. It can be used for different types of grinding operations. These include surface grinding, cylindrical grinding, and internal and external cylindrical grinding. CNC grinding machines are often used for processing precision parts. Such as molds, cutting tools, bearings, etc.
Applications
- Surface Grinding: CNC grinder machines are used to grind flat, parallel, curved, and contoured surfaces. It can improve the flatness and smoothness of the workpiece surface.
- Cylindrical Grinding: It is suitable for processing shaft parts, such as bearings, crankshafts, camshafts, etc.
- Internal and External Cylindrical Grinding: CNC grinders process internal and external cylindrical surfaces—for example, inner and outer circular bushings, roller bearings, etc.
- Sharpening: It is used for sharpening of tool knives. These include milling cutters, drill bits, blades, etc.
- Gear Grinding: It manufactures high-precision gears and improves their precision and wear resistance.
- Carbide Grinding: The CNC grinding machine is suitable for precisely grinding carbide cutting tools, molds, molds, etc.
- Hollow Grinding: It can be used to process workpieces with hollow structures. Such as pipes, bushings, etc.
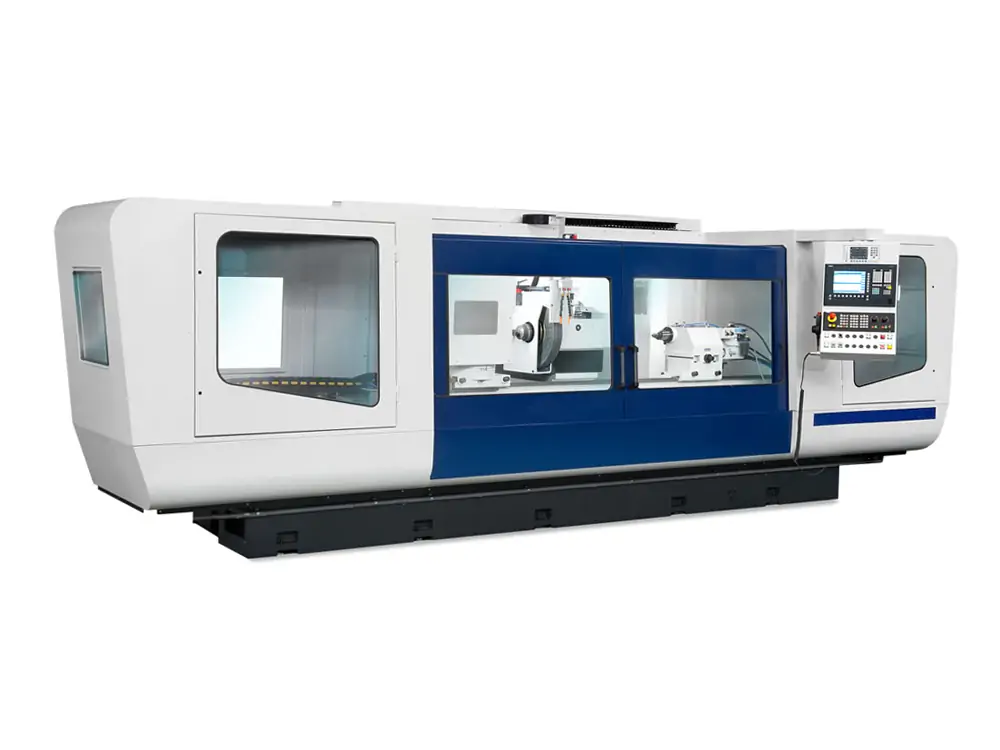
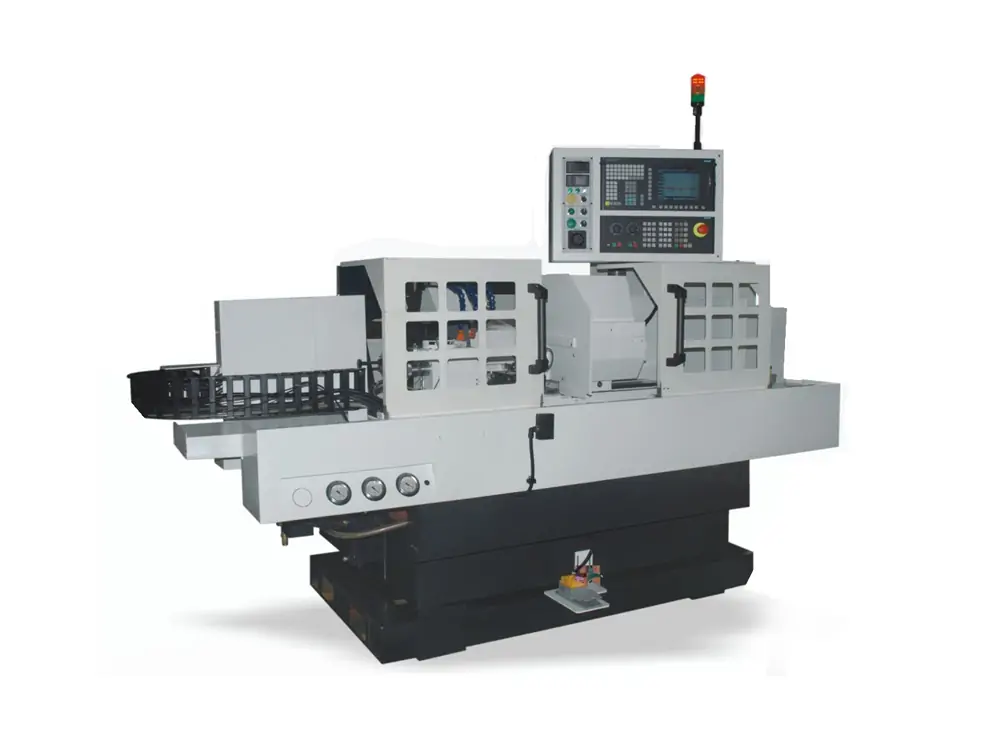
Pros
- High Precision: CNC grinding machine can achieve very high machining precision. It is suitable for workpieces with extremely high size and surface quality requirements.
- High Efficiency: Due to the high degree of automation, the processing process can be carried out continuously. It can improve production efficiency.
- Versatility: CNC grinders can adapt to different materials and machining requirements by changing tooling and process parameters. It has strong versatility.
- Complex Curved Surface Processing: A CNC grinder machine can complete the processing of complex curved surfaces. It is suitable for manufacturing parts with complex shapes.
Cons
- High Equipment Costs: CNC grinding machines are relatively expensive to purchase and maintain. It requires a more significant investment.
- High Operating Skill Requirements: A CNC grinder requires professional knowledge and skills. Operators need specialized training.
- High Environmental Requirements: CNC grinder machines usually have relatively high environmental temperature and humidity requirements. It needs to run in a relatively stable environment.
Type 4: CNC Punching Machine
CNC punching machines use CNC technology to control punch movement and beat table machine tools. It is used for stamping metal sheets. It realizes cutting, drilling, forming, and other operations on metal materials through pre-programmed instructions. CNC punch machines are often used to produce metal parts. It is widely used in electronics, automobiles, aerospace, and other fields.
Applications
- Electronic Field: It can produce electronic components, connectors, chassis, and other metal structural components.
- Automotive Industry: It is used in manufacturing auto parts. Such as body structure, chassis parts, interior parts, etc.
- Aerospace: It is used in aerospace manufacturing to produce metal components. Such as aircraft casings and spacecraft structures.
- Home Appliance Manufacturing: Metal casings, frames, and other components are used to manufacture home appliances.
- Construction Field: Used to produce metal components. Such as stair handrails, window frames, etc.
- Mold Manufacturing: It can manufacture metal molds and complete the stamping and forming processes of the molds.
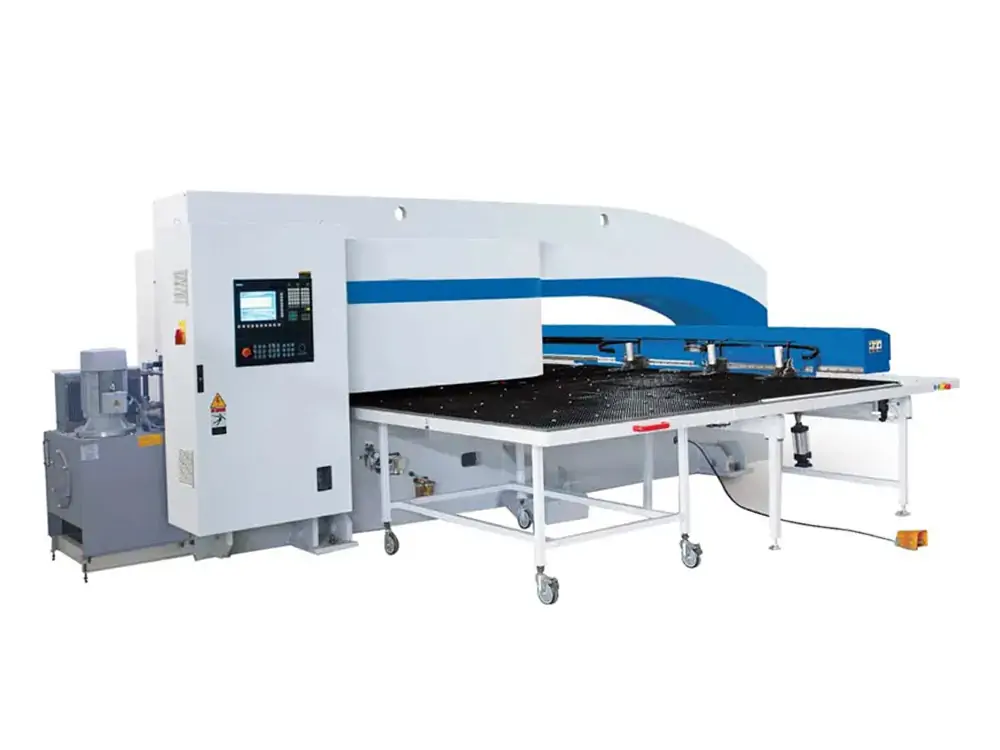
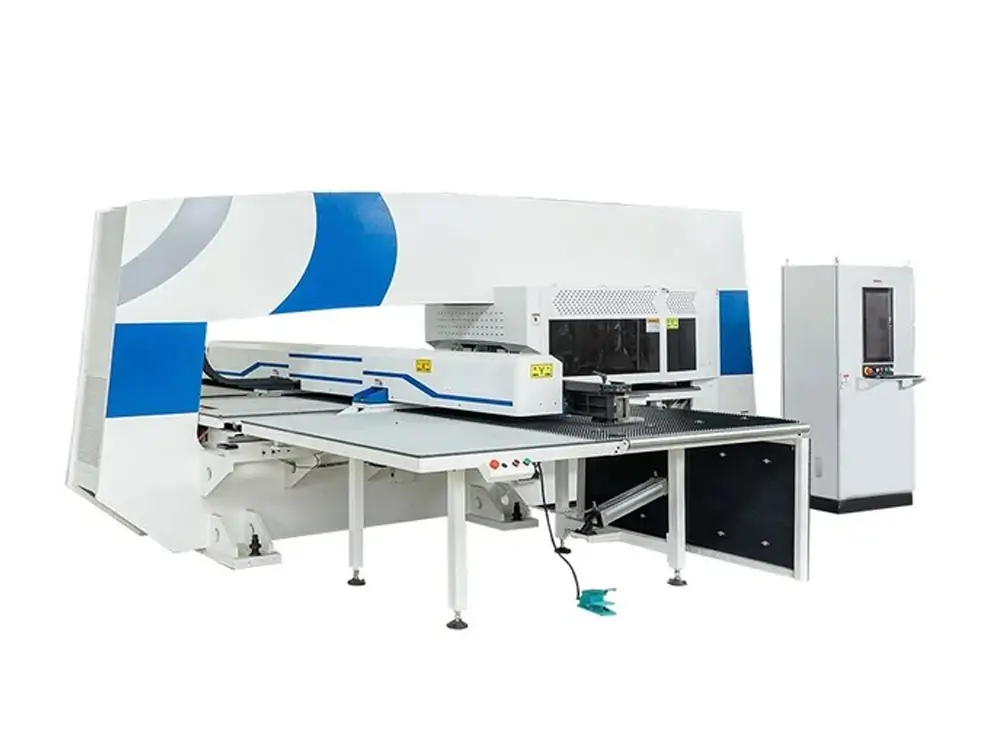
Pros
- High Efficiency: The CNC punching machine can quickly complete the stamping process of metal plates. It can improve production efficiency.
- Versatility: CNC punch presses can perform a variety of machining operations. These include punching, cutting, and forming. It can adapt to different processing needs.
- High Degree of Automation: CNC punch press machines can achieve automated production through pre-programming. It reduces manual intervention.
- High Precision: CNC punching machines can achieve high-precision processing under preset parameters. It ensures product quality.
- Suitable for Mass Production: It is ideal for mass production that requires high consistency of parts.
Cons
- Limited Scope of Application: The CNC punching machine is mainly suitable for stamping flat metal plates. The processing capabilities for curved surfaces or complex structures are relatively limited.
- Limited Tool Life: Punching tools will wear to a certain extent under high-frequency use. It requires regular replacement and maintenance.
- Higher Initial Investment: The acquisition and maintenance costs of CNC punch machines are relatively high. It requires a more significant investment.
- Not suitable for small batches and personalized production: CNC punch machines have a high degree of automation. It is more flexible than other processing methods for small batches and customized production.
Type 5: CNC Laser Cutting Machine
A CNC laser cutting machine is a machine tool that uses a laser beam to cut materials precisely. The laser cutting machine controls the movement of the laser head on the surface of the workpiece through a CNC system. It can achieve high-precision cutting of metal, plastic, wood, and other materials. This cutting method is used for production, manufacturing complex parts, and custom machining.
Applications
- Metal Processing: It can cut metal materials. These include steel, aluminum alloy, and stainless steel. CNC laser cutting machines are widely used in manufacturing industries. Such as automobile manufacturing, aerospace, electronic equipment, etc.
- Construction Industry: It can cut metal materials required for building structures. Such as steel structure, aluminum plate, etc.
- Electronic Manufacturing: Laser CNC cutting machines can produce high-precision parts. Such as electronic components, circuit boards, connectors, etc.
- Textile Industry: Laser cut CNC machines can cut textile materials. Such as cloth, leather, etc. It is used in the production of clothing and home furnishings.
- Medical Devices: It can be used to manufacture components for medical devices. Such as surgical instruments, medical device casings, etc.
- Crafts Manufacturing: CNC laser cutting machines can be used to manufacture handicrafts, decorations, and other finely processed products.
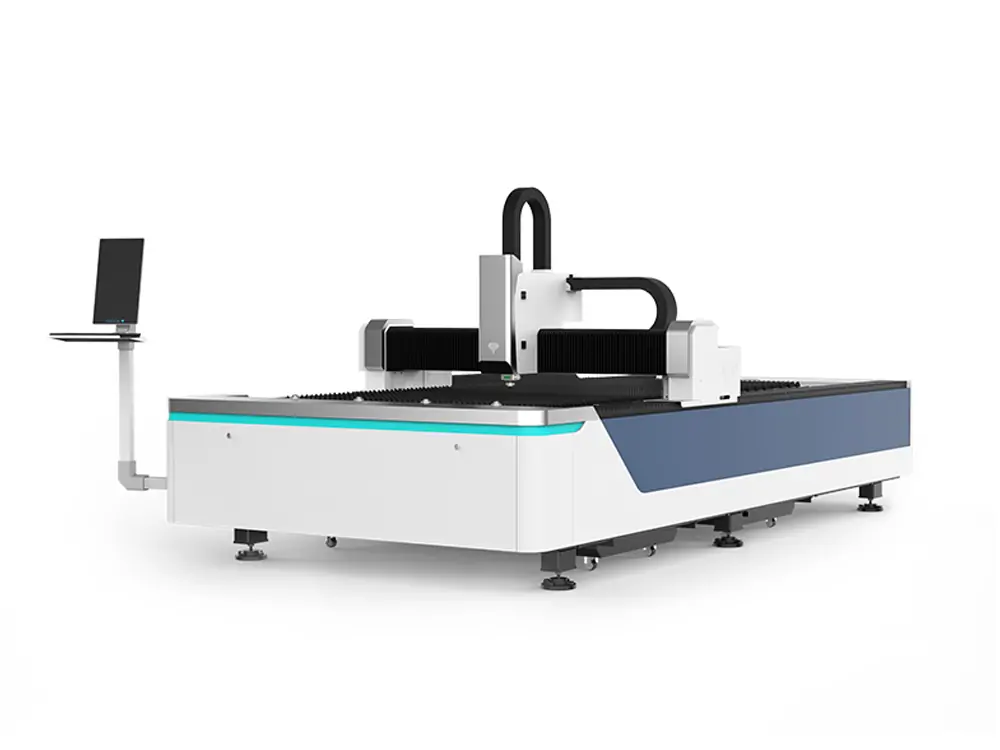
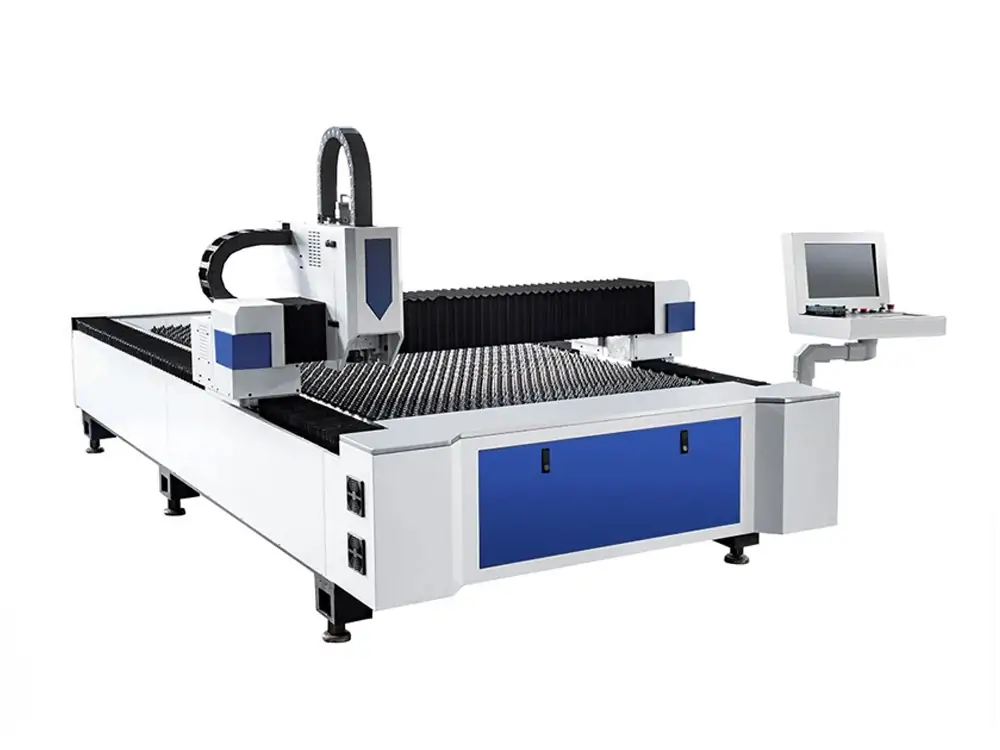
Pros
- High Precision: CNC laser cutting machines have very high cutting precision. It enables precise cutting of complex shapes.
- Non-contact Processing: Laser cutting is a non-contact processing method. It does not cause surface damage to materials. It is suitable for materials that need higher surface quality.
- High Efficiency: cutting speed is fast. It is ideal for high-volume production and requires no more tool changes.
- Suitable for Many Materials: CNC laser cutting is ideal for cutting various materials. These include metal, plastic, wood, etc. It has strong versatility.
- Flexibility: CNC laser cutting machines can adapt to workpieces of different shapes and sizes through program changes.
Cons
- Higher Initial Investment: The acquisition and maintenance costs of CNC laser cutting machines are high.
- Material Thickness Limitation: Laser cutting efficiency may be reduced for thicker materials. It is cheaper than other cutting methods.
- Sensitive to Light: Laser cutting requires a relatively good working environment. Light interference may affect cutting quality.
- Exhaust Gas Treatment: Smoke and exhaust gas will be generated during cutting. So you also need an effective exhaust treatment system.
Type 6: CNC Turning Milling Center
CNC turning milling center is a composite machine tool that integrates the functions of a lathe and a milling machine. It has two functions: a lathe that rotates the workpiece and a milling machine that cuts on the workpiece. It is controlled by a CNC system to realize multi-axis and multi-directional processing of workpieces. The design of this machine tool enables more complex and diverse processing tasks to be completed on one piece of equipment.
Applications
- Complex Parts Processing: It is suitable for producing parts with complex shapes and changeable structures. Such as engine parts, gears, etc.
- Mold Making: A CNC turning milling center is used to make molds and mold parts. It can complete the integrated processing of turning and milling.
- Aerospace Field: It is used to produce aircraft engine parts, aircraft structural parts, etc.
- Automobile Manufacturing: It is suitable for automobile engines, gearboxes, chassis, etc.
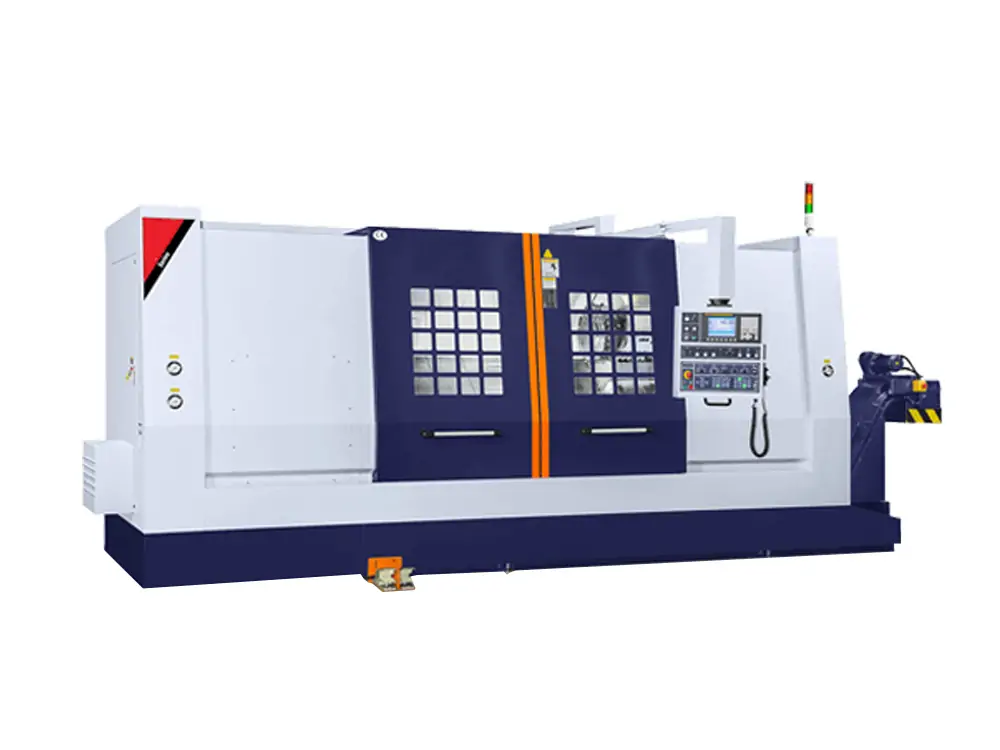
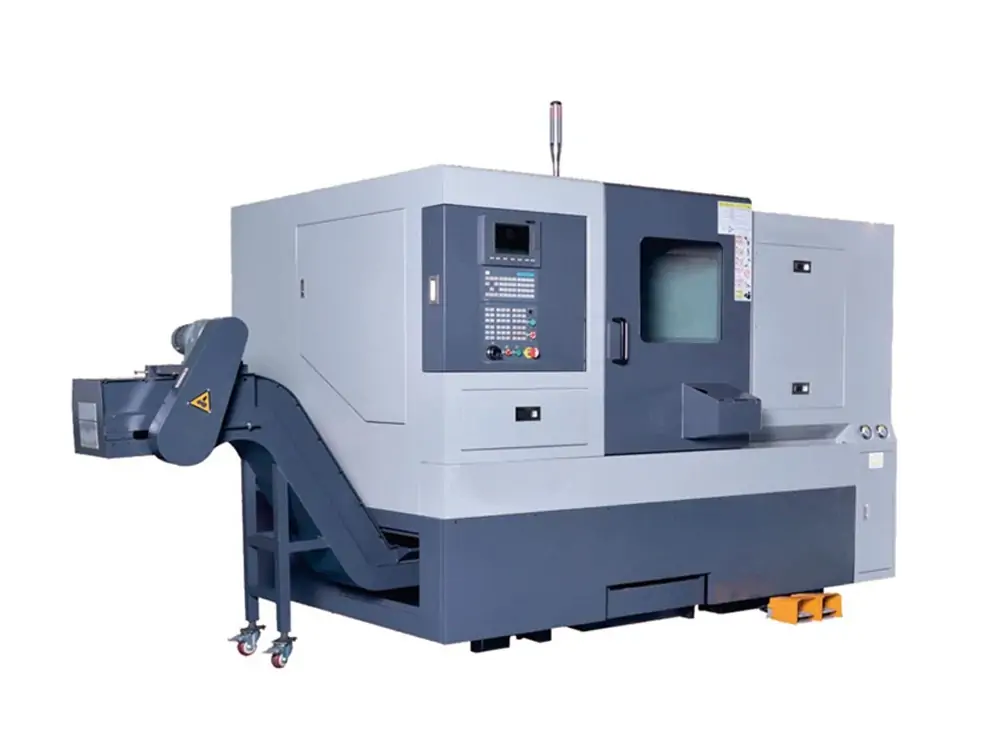
Pros
- Multifunctional Integration: CNC turn and mill machines integrate the functions of lathes and milling machines. It can complete many processing operations on the same equipment. It increases work efficiency.
- Space Saving: Mill-turn machines occupy a small area. It saves workshop space.
- High precision: CNC turning and milling machines are capable of high-precision machining. This is suitable for areas with high requirements on workpiece accuracy.
- Ideal for Small Batch Production: The flexibility of the turn-mill machine tool makes it suitable for small batch and personalized production. It can adapt to the processing needs of different workpieces.
- Reduced Clamping Times: It enables many processing steps to be completed on the same machine. It reduces the number of clamping times and improves machining accuracy.
Cons
- Higher Initial Investment: Compared with single-function machine tools, the buy and maintenance costs of turning and milling machines are high.
- High Requirements for Operators: Operating turn-milling machine tools requires certain professional knowledge and experience. It requires higher skills from operators.
- Limited Size of The Workbench: The workbench size is small due to the integration of two functions. It may limit the machining of large workpieces.
Conclusion
In this article, we look at the different types of CNC machines. From CNC milling machines, CNC lathes, CNC grinders, and CNC punches to CNC laser cutting machines and CNC turning and milling machines. Each CNC machine tool has its unique structure, working principle, and application fields. They have brought considerable changes to modern manufacturing.
CNC machine tools have become indispensable manufacturing tools in various industries. Not only do they improve product quality, they also provide manufacturers with more flexible and sustainable production methods. This guide helps you better understand all types of CNC machines. If you have any questions about the types of CNC machines, please get in touch with us.